The Greatest Guide To Alcast Company
The Greatest Guide To Alcast Company
Blog Article
The 6-Second Trick For Alcast Company
Table of ContentsSome Known Details About Alcast Company Unknown Facts About Alcast CompanyGetting The Alcast Company To WorkAlcast Company for BeginnersAlcast Company Can Be Fun For EveryoneOur Alcast Company Ideas
Chemical Comparison of Cast Light weight aluminum Alloys Silicon promotes castability by reducing the alloy's melting temperature level and improving fluidity throughout casting. Additionally, silicon contributes to the alloy's strength and wear resistance, making it useful in applications where resilience is critical, such as vehicle parts and engine parts.It additionally enhances the machinability of the alloy, making it less complicated to process right into finished products. In this way, iron contributes to the total workability of aluminum alloys.
Manganese adds to the strength of light weight aluminum alloys and improves workability. Magnesium is a lightweight aspect that provides toughness and effect resistance to light weight aluminum alloys.
Unknown Facts About Alcast Company
It allows the production of light-weight parts with outstanding mechanical buildings. Zinc enhances the castability of aluminum alloys and assists control the solidification process throughout spreading. It improves the alloy's stamina and firmness. It is frequently found in applications where intricate shapes and fine details are needed, such as decorative castings and certain automotive components.
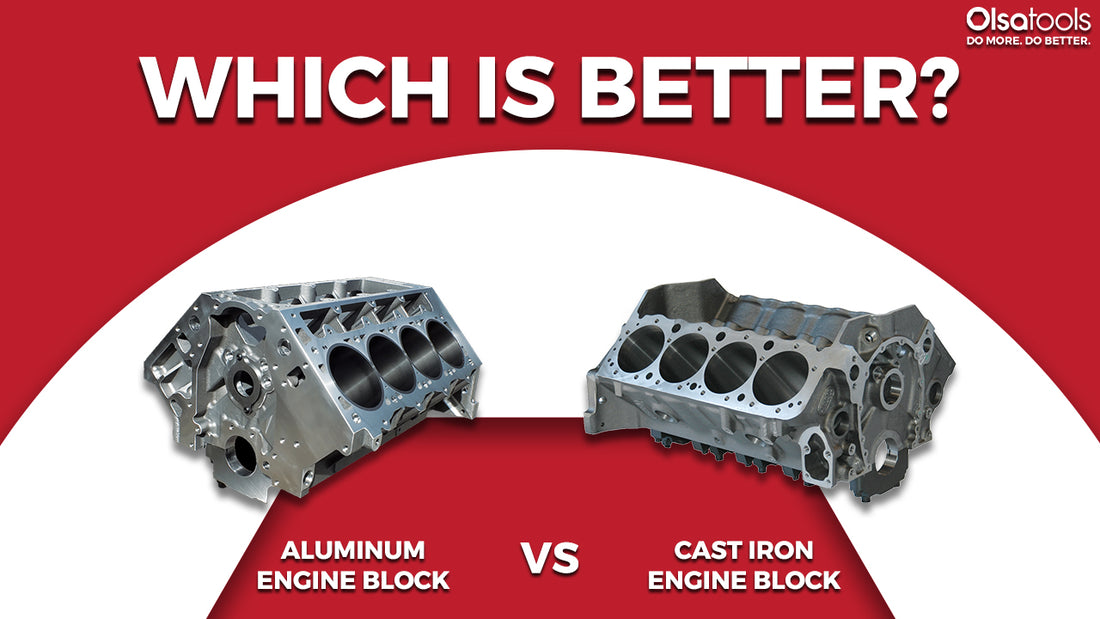
The main thermal conductivity, tensile toughness, return strength, and prolongation vary. Select appropriate raw products according to the performance of the target item created. Among the above alloys, A356 has the highest possible thermal conductivity, and A380 and ADC12 have the least expensive. The tensile limitation is the contrary. A360 has the best yield toughness and the highest possible elongation price.
Fascination About Alcast Company
In accuracy spreading, 6063 is fit for applications where detailed geometries and high-quality surface area finishes are vital. Instances include telecommunication rooms, where the alloy's premium formability enables smooth and visually pleasing layouts while preserving structural integrity. In the Lighting Solutions market, precision-cast 6063 components create stylish and efficient lights components that need detailed forms and great thermal efficiency.
The A360 exhibits premium elongation, making it excellent for complex and thin-walled parts. In precision casting applications, A360 is well-suited for industries such as Consumer Electronic Devices, Telecommunication, and Power Tools.
How Alcast Company can Save You Time, Stress, and Money.
Its one-of-a-kind homes make A360 a valuable choice for accuracy casting in these markets, improving item sturdiness and high quality. Foundry. Light weight aluminum alloy 380, or A380, is a commonly used casting alloy with numerous distinctive qualities.
In precision spreading, aluminum 413 radiates in the Consumer Electronic Devices and Power Devices markets. It's typically utilized to craft detailed elements like smartphone housings, video camera bodies, and power device housings. Its precision is exceptional, with limited resistances approximately 0.01 mm, making certain remarkable item setting up. This alloy's premium deterioration resistance makes it an excellent option for outdoor applications, making sure durable, sturdy products in the discussed industries.
The Best Guide To Alcast Company
The light weight aluminum alloy you pick will substantially influence both the casting process and the homes of the final find out here item. Due to the fact that of this, you have to make your choice carefully and take an educated technique.
Figuring out the most suitable aluminum alloy for your application will certainly suggest evaluating a large array of features. The first classification addresses alloy features that impact the manufacturing procedure.
Alcast Company Things To Know Before You Buy
The alloy you choose for die casting straight impacts numerous facets of the spreading procedure, like exactly how very easy the alloy is to work with and if it is prone to casting issues. Warm splitting, additionally known as solidification fracturing, is a normal die spreading problem for light weight aluminum alloys that can cause internal or surface-level rips or fractures.
Certain aluminum alloys are a lot more susceptible to warm fracturing than others, and your choice must consider this. It can damage both the actors and the die, so you need to look for alloys with high anti-soldering properties.
Deterioration resistance, which is already a noteworthy quality of aluminum, can vary significantly from alloy to alloy and is an essential particular to think about depending upon the environmental conditions your product will certainly be subjected to (aluminum casting company). Wear resistance is one more residential or commercial property typically sought in light weight aluminum products and can set apart some alloys
Report this page